What it is like to work with us
At Fjord Maritime, we are keen to be more than just a supplier to our customers. ‘Collaborating partner’ would be a more fitting description. Together, we will streamline energy consumption at your aquaculture facility and reduce both CO2 emissions and costs.
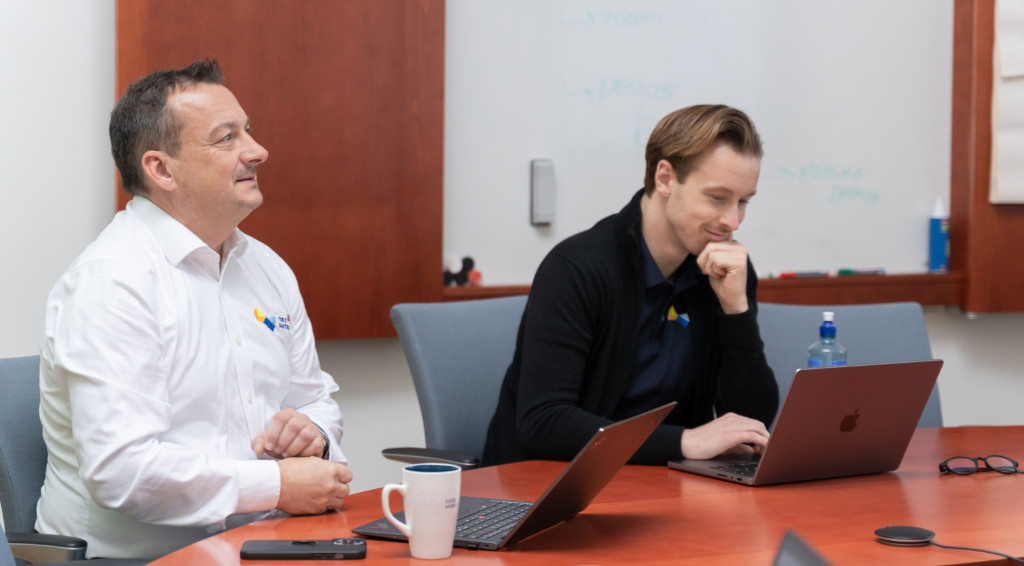
The first thing that happens when you get in touch with us is that we arrange an introductory meeting. This is the start of a potenial collaboration. At this meeting, we will map out your requirements while at the same time we can get to know each other better. The next stage is to collect information about the locality from the facility, including energy consumption, the size of the raft and the amount of fish produced.
Next, we prepare detailed analyses, a power profile of your energy consumption and a simulation of the running pattern of the diesel generator if using the hybrid solution. What will this cost you?
We also map out the opportunities for funding and help you with your application for support.
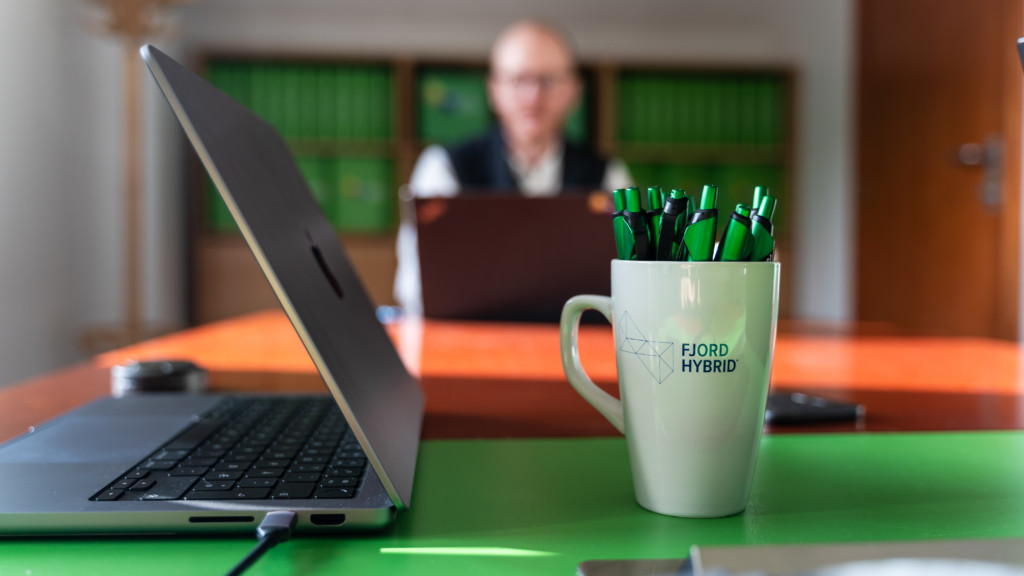
Together for zero emissions
Best of all for the climate is shore power combined with battery packs at the aquaculture facility. The hybrid system will ensure that you always have energy and can buy electricity when it is at its cheapest. When feeding the fish, use the battery rather than shore power. However, nature – or the costs associated with installing shore power – mean that this is not always possible. In these cases, we would install the hybrid solution alongside diesel generators, reducing CO2 emissions significantly.
Once we have laid out all the options, we draw up and present a proposed solution. We prefer to meet in person if possible, although of course this can also be done digitally. If you accept our proposed solution, we set up a firm offer. The next stage then is to review and sign the contract prior to installing the hybrid system.
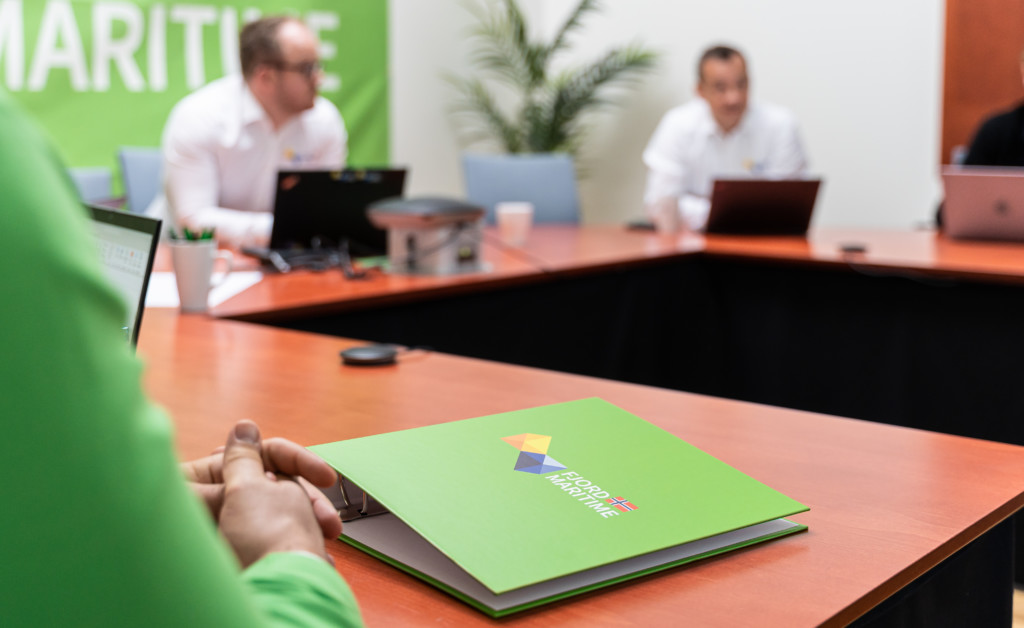
Installation and operation
Once a customer, you will move from our sales to our technical department, the department responsible for everything from coordination and delivery to the installation of Fjord Hybrid. One of our project managers will come and perform an inspection and will then arrange all the practical aspects in terms of transporting the equipment and a date for installation of the system.
Once installation time arrives, two installers will spent 4–5 days on the installation job. This will be done under production. Of course, all documentation and user manuals will be supplied. Next comes onboarding with Fjord Control, our system that provides you at all times with a full overview of all the technical activities at the facility while at the same time collecting environmental data. You will receive full training in Fjord Control. At present, the system is like a dashboard in a web version, but it will soon be available as a separate app for a mobile phone.
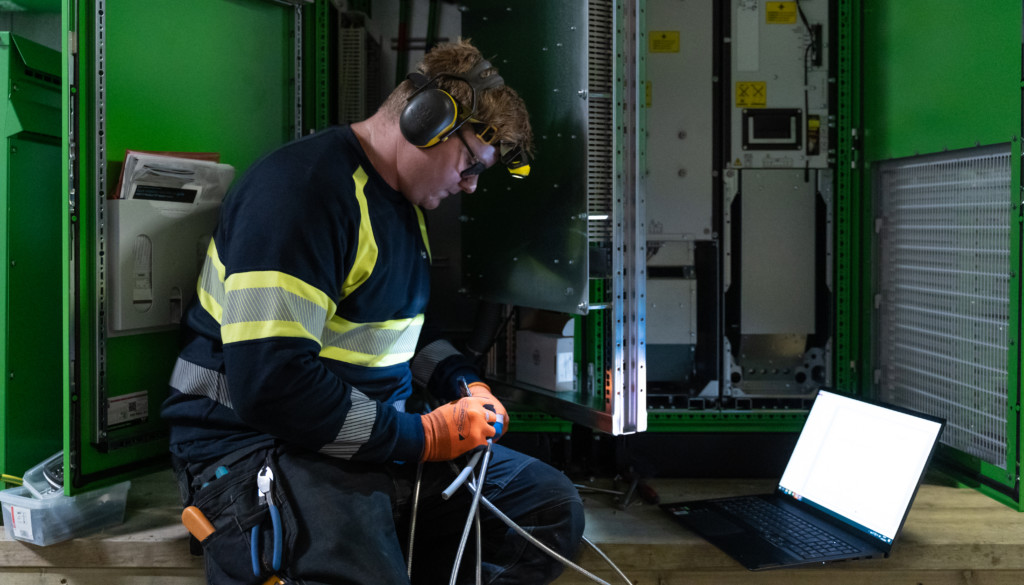
We monitor the hybrid system continuously
Safety is an extremely important factor when working with batteries and energy, and of course we take safety deadly seriously. We are continually developing our safety barriers to minimise the risk as much as possible.
In the vast majority of cases, we will discover any faults in the system before the customer does.
We will then contact you and fix the fault either remotely, where possible, or by physically travelling out to the site. As a customer, you will receive monthly reports and a summary from us twice a year. We will also conduct a quarterly technical review of the hybrid system.
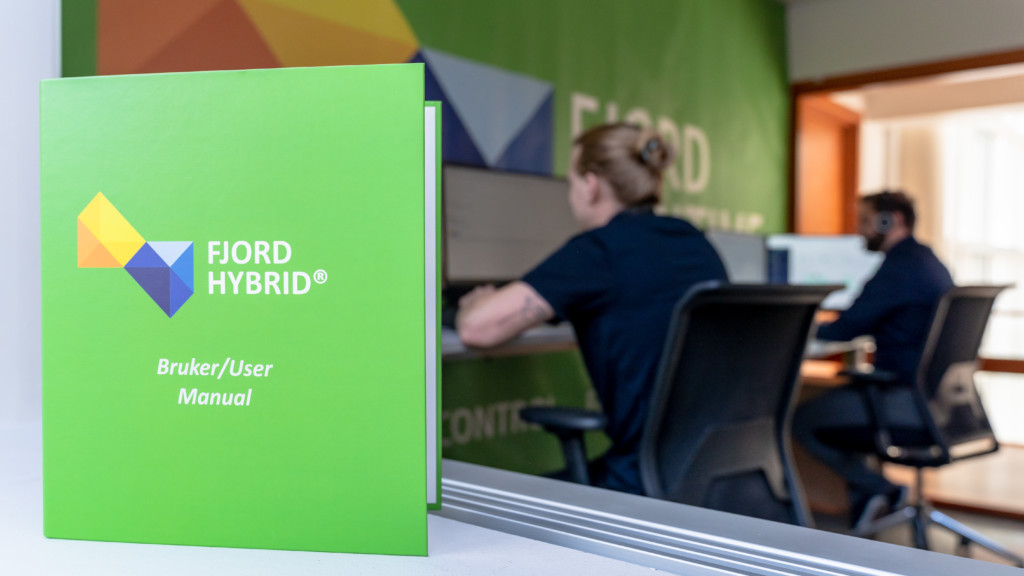
Fjord Hybrid is currently installed at over 180 aquaculture facilities in Norway, the United Kingdom, Canada and Chile. We always open new offices when we enter a market, as we are great believers in having a local base.
Are you interested in finding out even more about our unique hybrid solution for the aquaculture industry?
Complete the form below and we will then get in touch.